ToolConnect Saves $4,000 on One Simple Error
The Background:
In addition to integrating the full product line from Caron Engineering and developing our own production management and machine monitoring software, OnTakt, we also use these products every day for production machining.
Like every shop, we do our best to minimize where machine operators can make errors. Prior to having ToolConnect set up and running on our Fanuc RoboDrill we manually set tools and used a Renishaw tool setter to set the offsets in the machine. That simplifies the process but it didn’t eliminate ALL of the errors.
The challenge
Recently, on a weekend shift, a machinist noticed a bad surface finish on a high-volume production component. After further inspection of the part, it was determined that the last 6 parts had a poor surface finish. The result after a quality review and disposition was that those 6 parts were not recoverable and ultimately scrapped. Additionally, it took around 4 hours to diagnose and solve the problem with support from the engineering team.
The final diagnosis and fix for the problem was that the tool stick out for the ball end mill surfacing that area was measured to the collet nut on the tool holder. It was supposed to be measured to the face of the collet. The resulting extra stick out length caused the poor surface finish.
The Equipment:
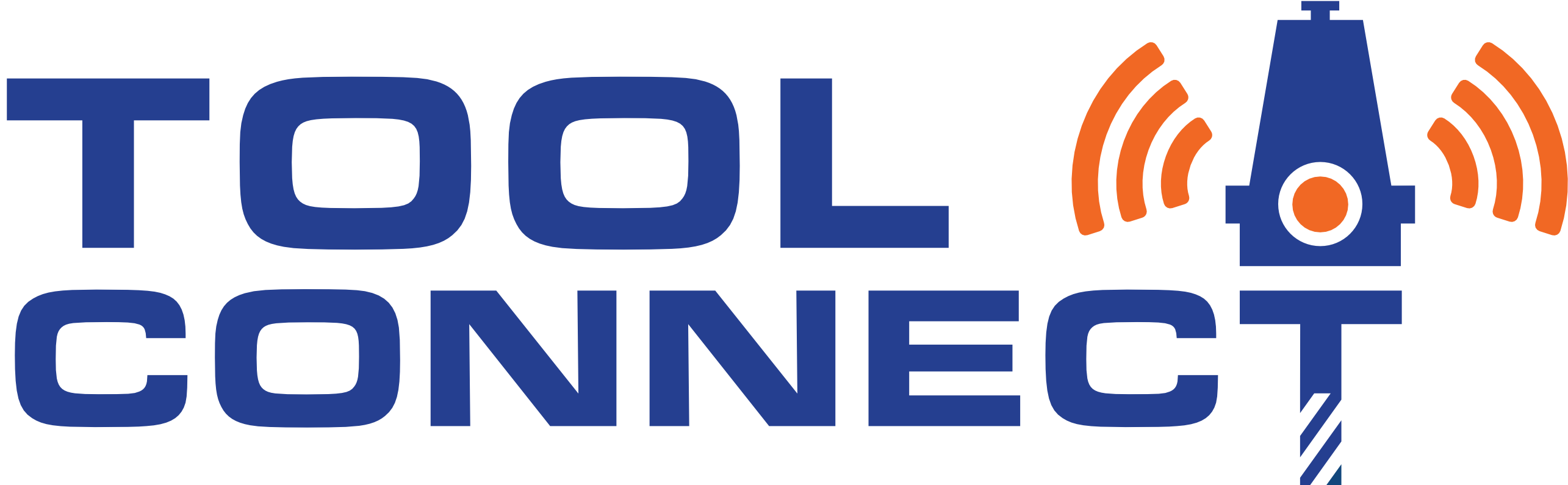
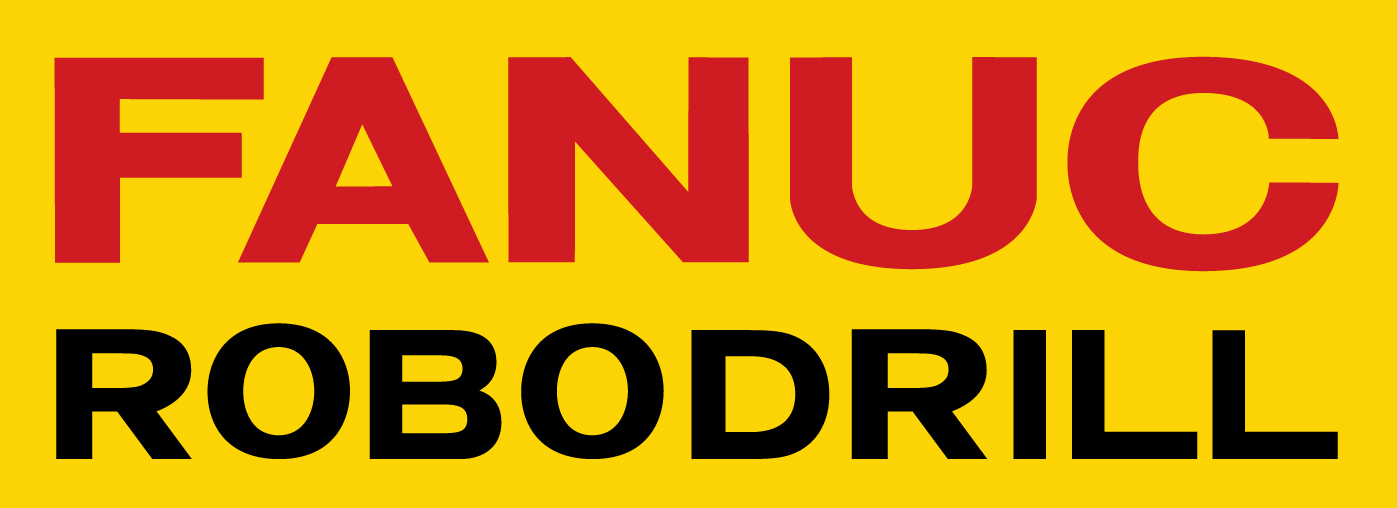
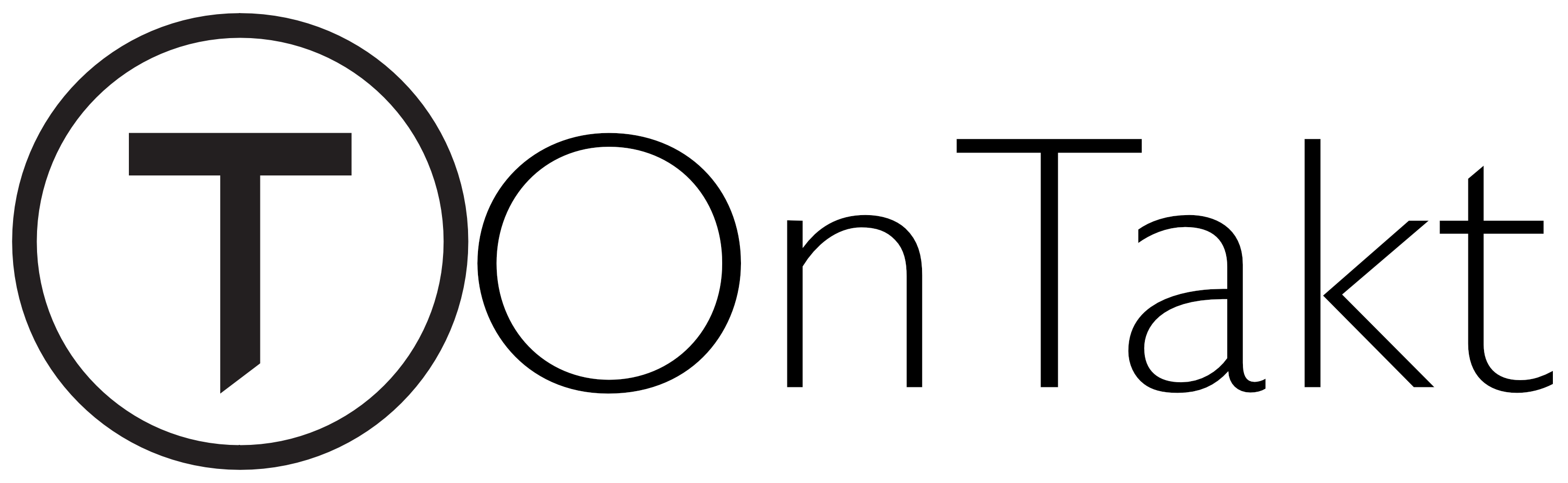
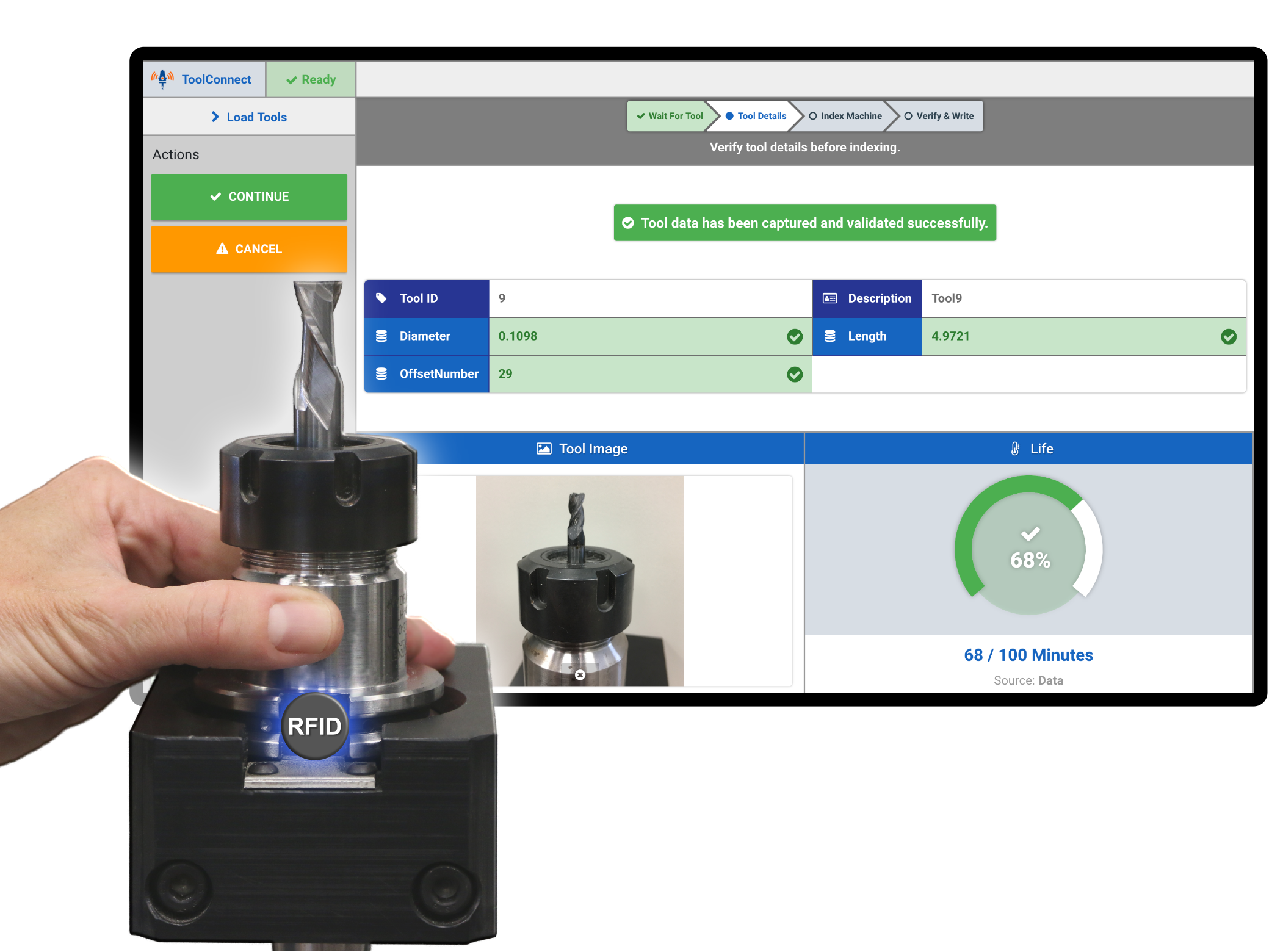
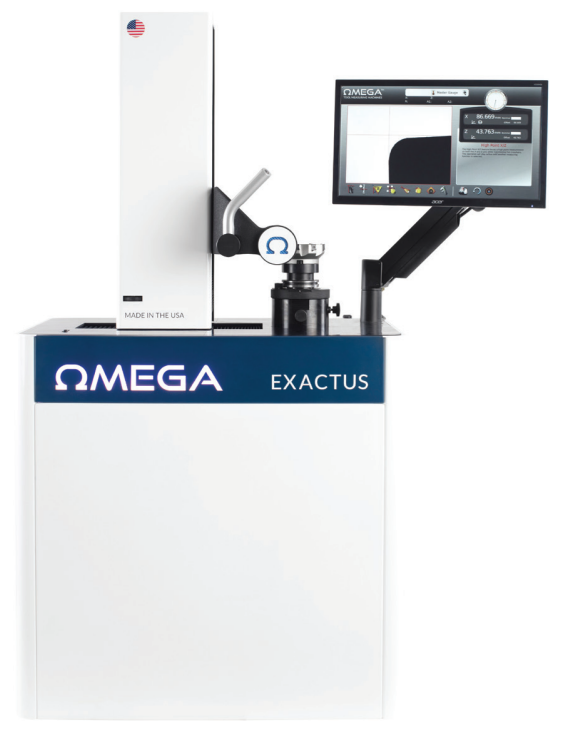
The Solution:
Wolfram’s OnTakt software makes it easy to manage tool offsets and capture instructions for how to build a tool. But, the tool management module alone doesn’t completely eliminate operator error. How do we make sure this doesn’t happen again? That’s where ToolConnect from Caron Engineering saves the day.
ToolConnect allows us to use Omega TMM’s Exactus Pro tool presetter to setup tools outside of the machine. The Omega TMM Exactus Pro records the tool offset data and stores the data on an RFID chip inside the tool holder. When the tool is transferred to the RoboDrill for loading, the tool is placed into an RFID reader and Caron Engineering’s ToolConnect automatically loads the data into the RoboDrill control offsets. This process workflow eliminates operator errors commonly caused by mis-entering data saving significant time and money.
But more importantly, in our case, ToolConnect can validate the tool length being loaded into the machine. In this example where the tool was longer than it should have been due to a measurement error, ToolConnect would prevent the tool from being registered in the machine and force the operator to intervene.
The Results:
ToolConnect saves $4,000 on simple errors.
- By having the machine down for 4 hours for troubleshooting we were not making parts and losing the revenue generated by running the RoboDrill continuously.
- During the downtime several engineers were involved with solving the problem taking away engineering resources from other valuable projects.
- The real savings comes from the scrapped parts. Scrapping 6 parts, near the end of the manufacturing process, is a cost that could have been easily avoided with ToolConnect.
Caron Engineering’s cutting-edge machine tool process technologies, coupled with premium machine tool solutions, and the combined support, training, and applications expertise from Wolfram Manufacturing have provided the metal cutting manufacturing industry with unparalleled productivity, reliability, and cost effectiveness.