THE CHALLENGE
Here at Wolfram, we’re not just an integrator of Caron Engineering’s Tool Monitoring and Adaptive Control (TMAC) product, we’re a production machine shop
running 24/7. We use the Caron products every day (and all night too) to save money on tooling costs.
Prior to introducing TMAC onto our machines we knew we were spending more than we should by being conservative with our tool counting. We would conduct tool studies to determine how long we could safely run a tool. Like many shops we talk to, we found that there was significant variation in tool life from tool to tool, especially with different lots of material. One tool run might find us with a tool life of 75 parts, another 150 parts. The wide range of tool life variation in our tool studies meant we were replacing nearly all our tools prematurely, leaving money on the table
THE EQUIPMENT
Tool monitoring and adaptive Control
Okuma LB3000 EXII CNC Lathe
Production management software
CB3 UR10 picks 1 part / 24 minutes
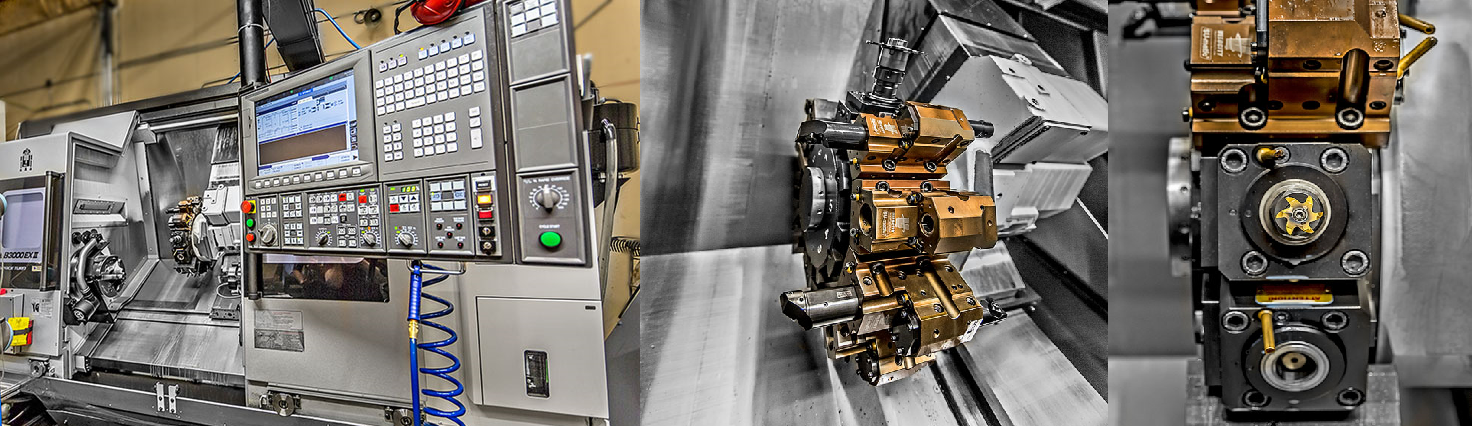
THE SOLUTION
One of the things that originally drew us to Caron Engineering was their TMAC product. Like most shops running production we want to maximize the life of our tools, but we also don’t want them to break causing scrapped parts, misaligned tooling, or even worse, a damaged spindle. This is a fine line to walk and we tended to be conservative… paying a bit more for tools that get changed before they break is cheap insurance to prevent a costly spindle repair or to lose valuable uptime on a machine.
The solution for us was Caron’s TMAC. TMAC can monitor the horsepower of the machine and we are able to set limits for each tool. So, if a tool starts to wear, the machine will stop so we can change out the tool. If a tool does break, it will stop immediately saving further damage to the part, misaligned tooling, or spindle damage.
THE RESULTS
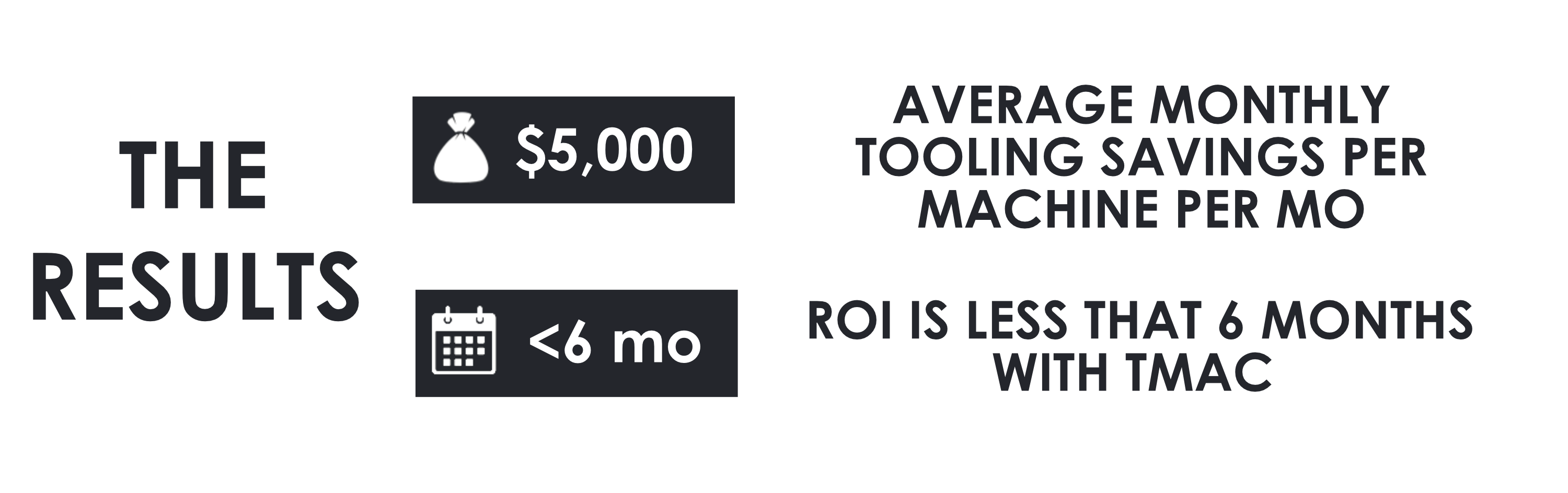
Automating your manufacturing processes doesn’t have to mean robots! While robots are a great tool to have available, we’ve found that there are opportunities to increase profitability with lower up front capital costs. What would you do with a significant reduction in tooling costs like an extra $5,000 per month? With a return on investment under 6 months you can see why we run TMAC on every CNC in our shop.
If you’d like to talk to learn how we can help you increase productivity and profitability of your shop OR if you’d like to see TMAC live in a production environment at our Production Technology Center, then click below to connect with an expert.
Wolfram Manufacturing is both a working production machine shop and a technology consulting firm helping OEM’s with tools like adaptive machining. Wolfram Manufacturing, at its founding in 2011, was an extremely versatile machine shop that specialized in medium to high volume production of metal parts. Wolfram focused on using the best technology manufacturing had to offer and appealing to the next generation of makers. Still operating a full production shop, Wolfram has expanded to offer consulting, training, and distribution of 3rd party hardware + software solutions to help their customers reach the next level. Wolfram Manufacturing exists as a place where ideas, innovation, and practical application come together to make the manufacturing world better.