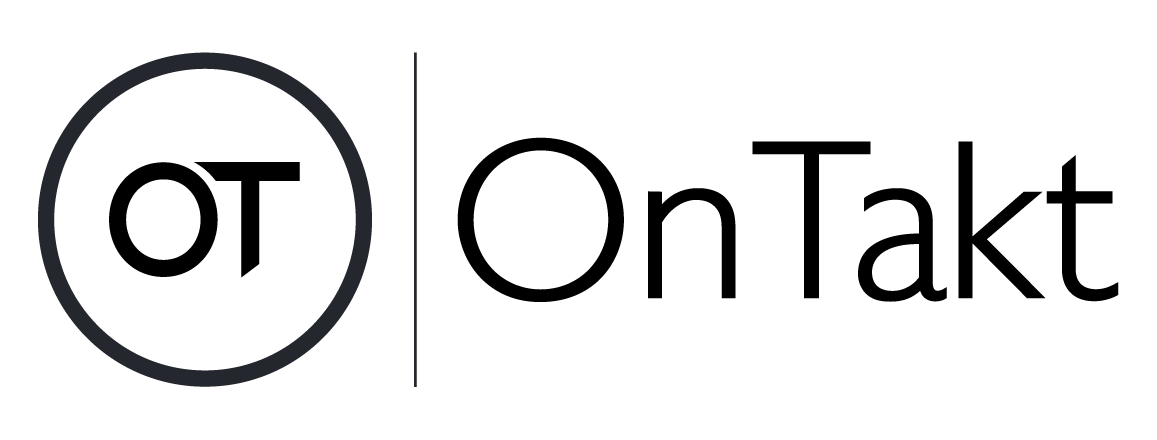
Increase Production Efficiency
Use OnTakt to Identify and Justify Automation
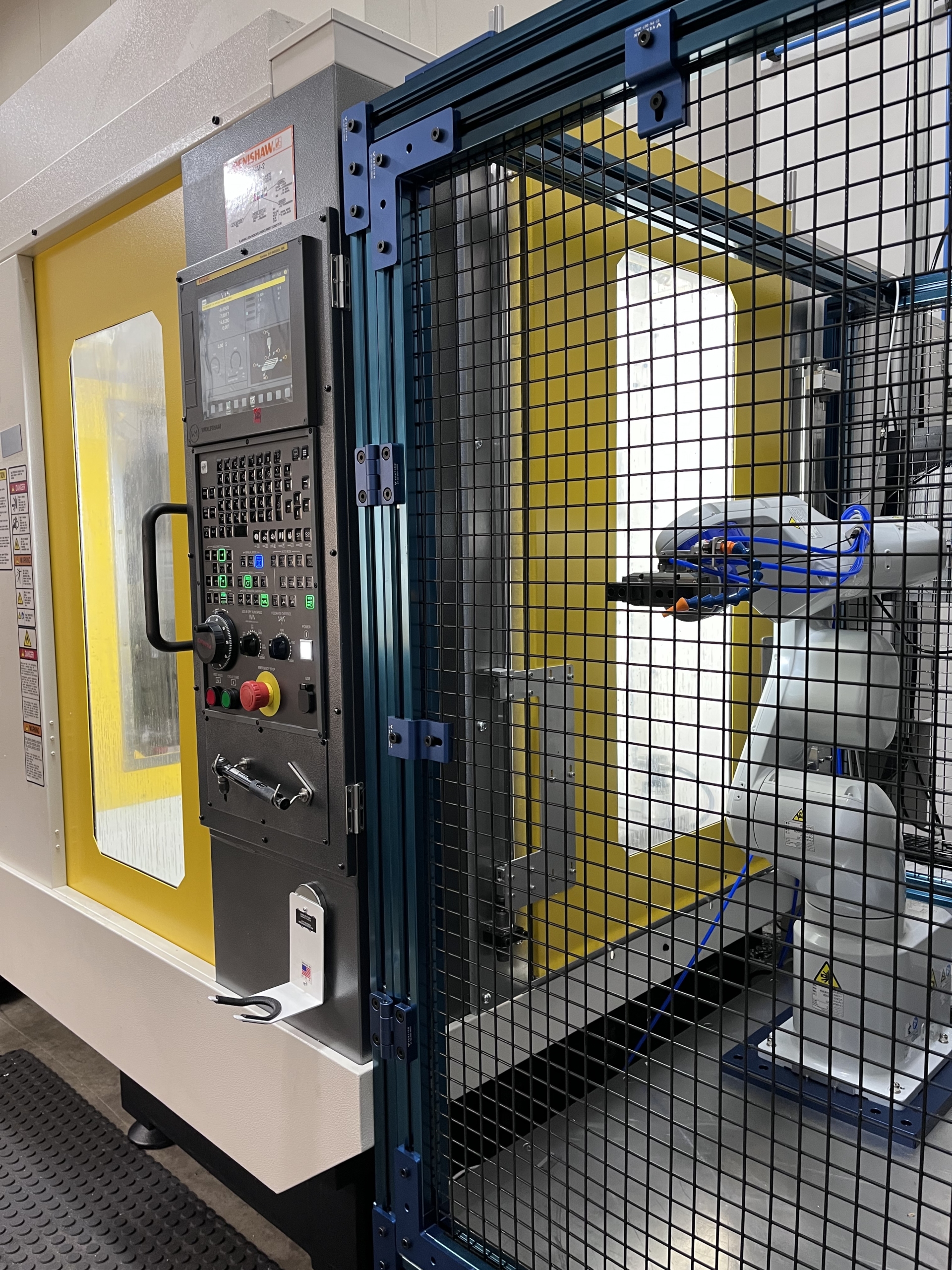
OnTakt’s real-time data will enable you to increase production efficiency by increase uptime systematically and permanently. Capturing all of your production data over time also allows you to historically review performance and highlight opportunities to add additional automation or equipment to get more out of your existing machines. Looking for patterns in historical data can lead to rapid ROIs for machines with poor run quality or that require significant manpower to run. OnTakt makes it easy to access historical data to define automation projects and provide the data necessary to calculate the ROI for an improvement to your shop.
COST SAVINGS WITH ONTAKT
$76,725
$76,725
COST OF AUTOMATION
75%
REDUCED OPERATOR ATTENDANCE AT MACHINE
2X
THROUGHPUT OF A $75 PART
1
MONTH
USEHISTORICAL DATA to identify opportunities to leverage automation to increase production efficiency
JUSTIFY NEW EQUIPMENT by using production data to perform ROI calculations